物流業界は今、大きな転換期を迎えています。
2024年問題として知られるこの課題に直面する中で、各社はどのような対策を講じるべきでしょうか。
このシリーズ「5分でわかる『2024年問題とその対策』」では、2024年問題への様々な具体的な対策について解説します。
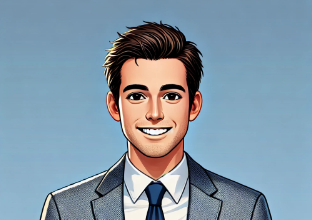
前回の第8回では2024年問題改善に向けた具体的な対策について解説しました。今回の第9回でも引き続き具体的な対策について詳しく解説します。
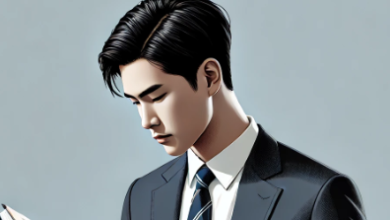
今回は具体的な対策として、出荷に合わせた生産・荷造り等についてです。
出荷に合わせた生産・荷造り等
- 概要
-
トラックドライバーの荷待ち時間を増やす原因として、荷積みの際の非効率性が挙げられます。これらの作業を効率的にすることで、ドライバーの荷待ち時間を削減することができます。
- メリット
-
荷積み時間の短縮:出荷順や出荷時の荷姿を考慮して製造順や荷置きを行うことにより、ピッキングや製品の無駄な移動を不要とし、積み込み時間を短縮することができる。
在庫管理費用の縮減:出荷に合わせた生産体制に移行することで、荷主にとってが製品在庫削減によるキャッシュフローの改善や、在庫管理費用の縮減などの効果がある。
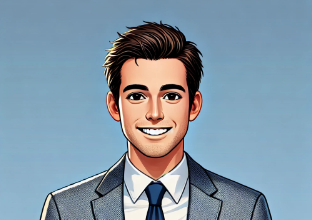
次に参考事例について詳しく解説します。
参考事例:集荷、荷纏め体制の見直しによる積み込み時間の削減(石川県)
事例の概要
石川県で従来は生産順に保管していた集荷品を出荷順に保管したことで、積み込み時間、荷待ち時間を縮減した事例
成功のポイント
荷主とトラック運送事業者で現場の問題点を確認・改善実施することができた
荷主の協力により、出荷に合わせた物作りが実現された
荷主とトラック運送事業者の、日ごろの信頼関係
改善前の状況
トラック一台あたりの積み込みにかかる時間は約90分だった。なぜなら、出荷にあわせた生産体制ではないためピッキング作業が多く、集荷品の取り纏めが複雑となり積み込み作業に時間を要していた。
改善後の状況
改善前と比べて、約40分の時間短縮である50分で一回当たりの積み込みができるようになった。
出荷に合わせた生産体制を確立、ピッキング作業の減少と車両にあわせた取り纏めにより積み込み作業時間が削減された。
課題
出荷に合わせたせいさんたいせいではないため、部品が完成のたびにピッキングが発生している。ピッキング回数が多くピッキング作業と荷纏め作業が分業となっており、積み込み作業において荷纏めを伴う作業が発生し作業時間が長くなる。
- 問題点
-
1 出荷場所は、できあがった製品から積み上げ
2 パレット数も多くサイズがバラバラ
3 ピッキングは出来上がったもの順
4 出荷の荷姿がわからない - 事業内容
-
出荷に合わせた生産体制の確立
・出荷情報の見える化、出荷日から逆算しリードタイムを考慮し生産を行う出荷の平準化
・午前・午後と平準化して出荷を行うトラックに積み込む順番でピッキング・荷纏めを行う
・ピッキング作業~荷纏め作業のワンオペレーター化
・トラックに積むに姿を決めてピッキング パレットサイズ・荷の高さ・順番を考慮
・パレット数を少なくして積み込み回数を減少
結果
積み込み作業時間の40分の短縮
入庫から出庫までの時間を平均38分の短縮
荷主企業のメリット
製品在庫削減によるキャッシュフロー工場
倉庫管理費減少
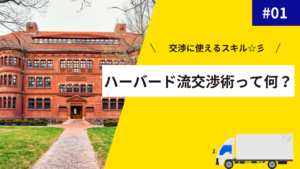
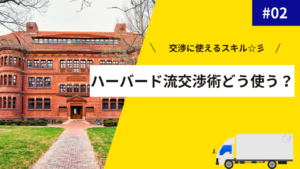
\「FC車両リース」の詳細はこちら/
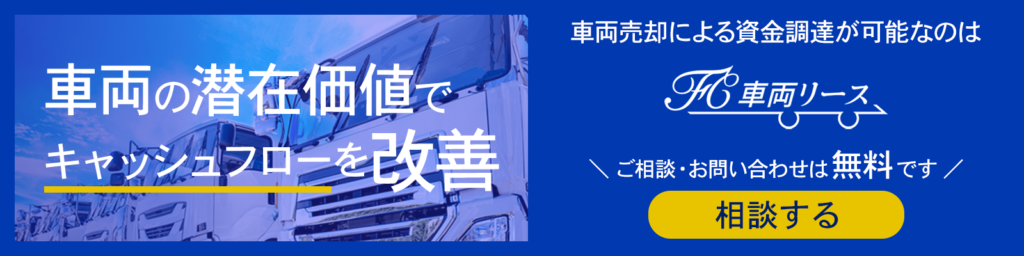
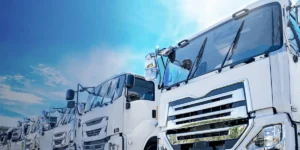
まずはお気軽にお問い合わせください!
まずはお気軽に
お問い合わせください!
TEL 03-5212-5197
お見積もりの際は次の資料をご用意ください。
・決算書(直近3期分)
・車検証
・既存リース契約のわかるもの(契約書・お支払い明細の写し 等)
※お見積もり、審査は無料です。
提携企業さま、または直接弊社にお問い合わせください。